Use Case Description
Background
Thiamethoxam is a broad-spectrum insecticide used for a variety of crops. Commercial-scale production of thiamethoxam involves the reaction of raw material, followed by distillation, and then crystallization.
Thiamethoxam yield can depend on several factors including the molar ratios of raw materials entering the reactor, the duration of the reaction, the amount of catalyst, the amount of byproducts formed in the reaction, the pH of the neutralized solution, and the reactor and distillation operating conditions such as temperatures, pressures, and flow rates.
Problem
The yield of thiamethoxam can vary significantly, typically ranging from 65-90%. This variation is mainly due to variability in the composition of the raw materials and the operating conditions during each step of the synthesis and separation process.
Process and quality engineers in the plant must promptly identify the factors that could lead to lower than expected yields and determine how to modify process settings to mitigate these effects.
Simultaneously optimize dozens of process condition to proactively maximize yield of pesticide production, while mitigating byproduct formation.
The current approach to address this issue is often through a Six Sigma-based method. The process engineer analyzes data to spot variations in raw materials or process conditions among the numerous indicators, or tags, within the customer’s Process Information Management System (PIMS). However, these methods might not fully capture the complex interrelations between tags, potentially missing the root cause of the lower yields in a batch.
This oversight can result in several consequences:
- Financial loss stemming from the excessive use of raw materials and the need for extra handling of waste, such as solvents and undesirable byproducts.
- Reduced revenue due to yields that fall short of expectations.
- Prolonged periods spent on diagnosing the problem and applying modifications to the process.
Fero Labs Solution
Plant operators can employ Fero to fine-tune operational parameters, ensuring high yield despite varying raw material compositions and operating conditions throughout the synthesis and separation processes. Fero provides the capability to predict and maximize the final product yield by optimizing the factors influencing yield. It also aids operators in pinpointing specific operating regimes that contribute to lower-than-expected yields, facilitating targeted process-level changes.
A “Live Fero Analysis” for this use case presents two screens:
- Detailed View: for plant operators to monitor production and take action at any moment. Here, Fero recommends how yield can be maximized under current production conditions. Restrictions can be placed on the maximum or minimum allowed values for raw materials, enabling engineers to safely explore cost minimization objectives while continuing to maximize yield.

- Simplified View: for plant operators to know exactly what action to take to maximize yield and reduce raw material consumption.
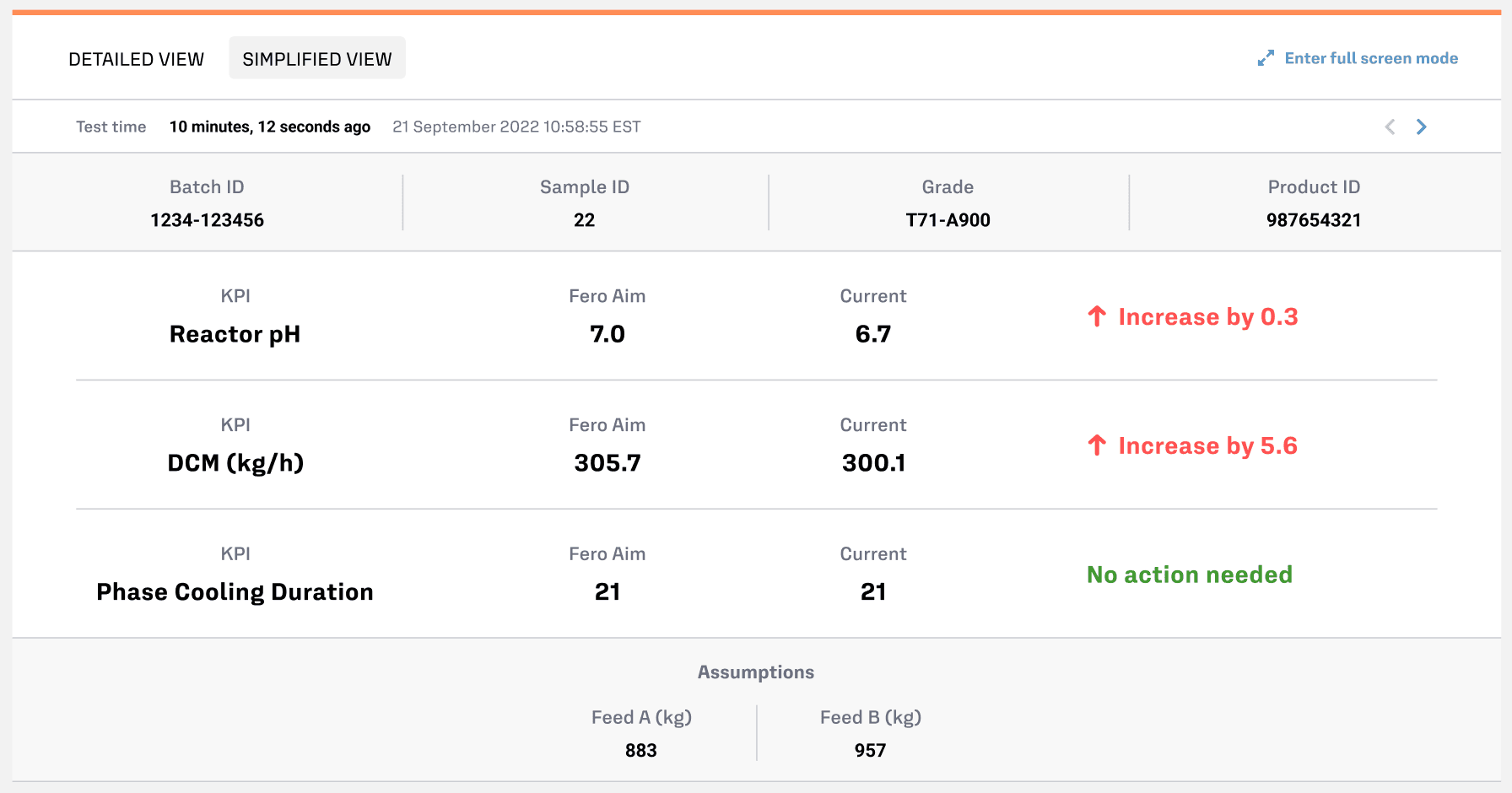
Additionally, process engineers can use Fero’s “Group Prediction Simulator” to simulate various “what-if” scenarios of process settings changes to increase the yield of historically low-yield batches.

Process & Business Outcomes
Optimize process parameters for maximum batch yields
Fero Labs equips operators with the tools to fine-tune each batch's process parameters. A full deployment of Fero across operations can improve yields by up to 10% per batch.
Identify the root causes of lower-than-expected yields for targeted improvement
With Fero's Root Cause Explorer, plant engineers can swiftly identify which variables impact yield—often within minutes. Utilizing Fero enhances overall process comprehension, allowing the team to rapidly determine the most influential factors out of hundreds that affect batch yield and their impact on the relative change in yield.
Conduct 'what-if' simulations to gauge the effects of process modifications
Fero's Group Prediction Simulator lets the plant engineers test hundreds of different “what-if” operating scenarios for batches with low yields. This feature assists plant managers in adjusting relevant process set-points across the entire operation. Such adjustments can save plant engineers several days or even weeks of analysis, which can now be more efficiently addressed thanks to this feature.
Fero Labs Adoption Timeline
Plant teams can collaborate to set up and deploy Fero Labs. Below is a timeline highlighting typical steps. With Fero’s easy-to-use, no-code interface, this can be achieved in a matter of weeks, not months or years.
Data Requirements
Plant teams can collaborate to set up and deploy Fero. Below is a timeline highlighting typical steps. With Fero’s easy-to-use, no-code interface, this can be achieved in a matter of weeks, not months or years.
Activating This Use Case
Consider our Industrial Use Case Playbooks as inspiration and tactical ideas for your team to align on to maximize the efficiencies of your plant.
Each Playbook has a matching Use Case Blueprint which provides more detailed steps to activate each use case within the Fero Labs platform.
If you’re curious to see these in action please book a free feasibility study with our team!
Together, let us continue to push the boundaries of what's possible, driving towards a future where industrial manufacturing is not just efficient and sustainable but truly transformative in its impact on society and the world at large.
Thank you for joining us on this journey, and we look forward to continuing to partner with you in your pursuit of excellence.
Download the entire Pesticide Batch Yield Maximization Playbook to access additional tables and details about this industrial use case.