Use Case Description
Background
Before the release from production facilities, newly produced batches of consumer goods products such as shampoos and body wash products, must pass rigorous quality assurance testing. This end-of-line testing often involves manually taking samples and testing them in labs. Quality assurance tests are critical to ensure that products meet the required stability and safety specifications, and that they possess properties such as viscosity, pH, odor, and feel to meet consumers expectations.
Problem
Batch release protocols significantly influence the daily production capacity of manufacturing facilities due to the time, effort, and complexity involved in completing quality assurance tests. Furthermore, batch release testing can be costly with lab facilities, capital expenditure, and many Full Time Employee (FTE) positions needed to carry out these tests. Batches that do not meet batch release criteria may require reworking or disposal, further affecting profits.
Optimize production parameters in real-time to maximize batch acceptance rates.
Typically, beauty care production plants have a batch acceptance rate around 95%. However, this rate can vary significantly across different facilities. Batch acceptance can be affected by the type of formula being produced, the stability of raw materials in different environmental conditions, and the experience and quality standards of the production plant. Consequently, despite several plants producing identical products and operating under the similar operational procedures, the final quality of these products can differ substantially.
Click here to download the entire Playbook
Fero Labs Solution
Process engineers can use Fero Labs software to adapt process parameters during online production, adapting to variation in raw material and target product specification.
As a specific example, Fero Labs software can be used to predict the viscosity of a final shampoo batch during production. Optimizations are then configured to share process recommendations with plant operators so that they can take concrete steps in real-time to control for final product viscosity and ensure batch release criteria are met.
A Live Fero Analysis for this use case presents two screens:
- Detailed View: for production and quality engineers to monitor production and take action at any moment. In this example we see that Fero predicts it is possible that the final product viscosity will exceed the upper limit and as such recommends changing homogenizer speed to ensure in-spec production
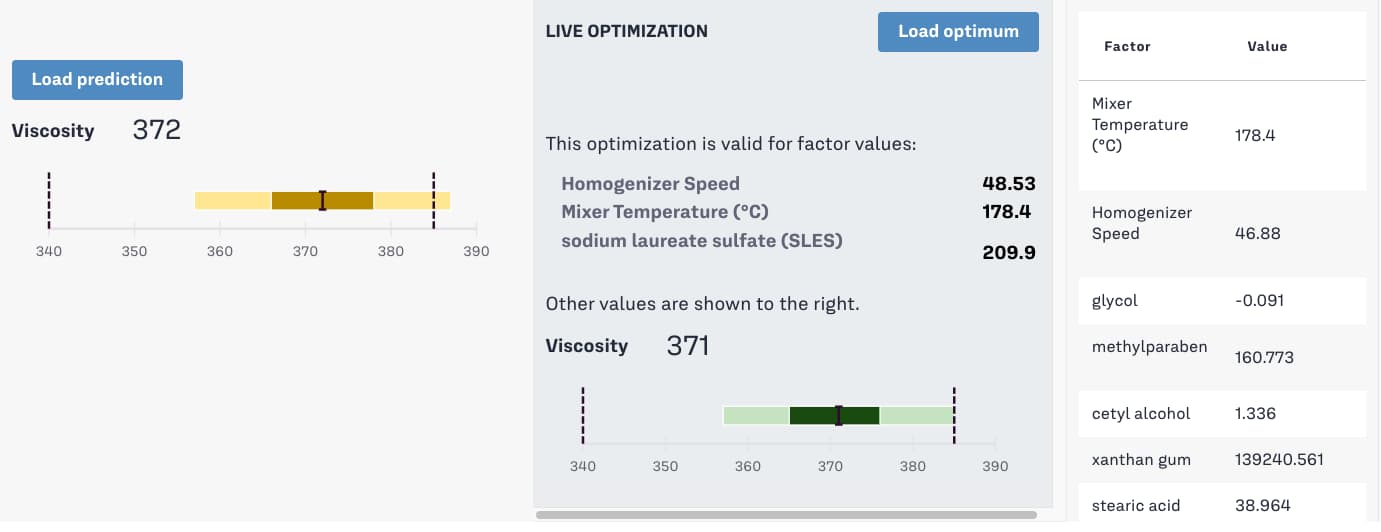
- Simplified View: for plant operators, with critical information clearly presented to prompt them to make changes to the process.
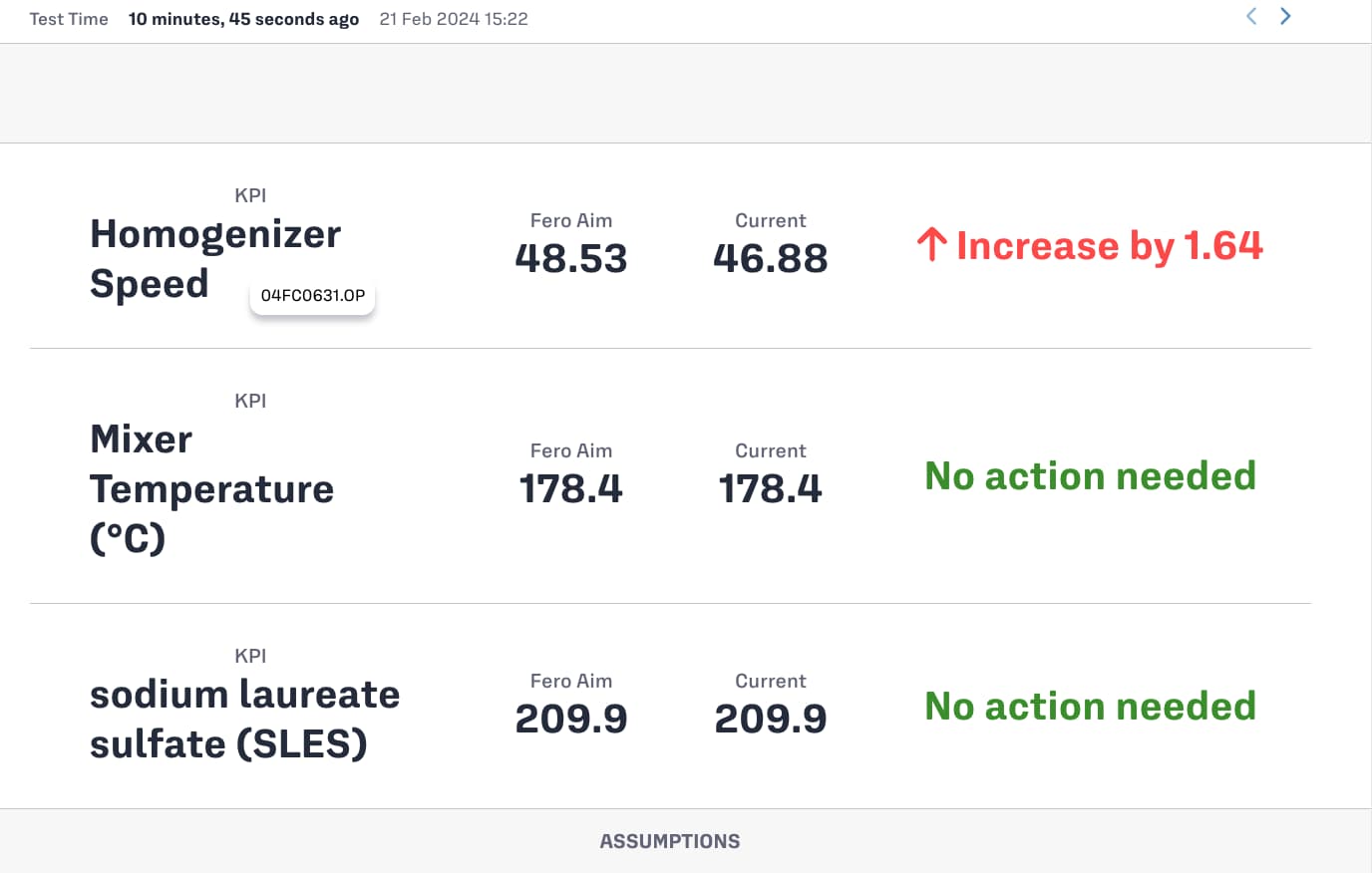
Process & Business Outcomes
Reduced lab measurement frequency
Successful real-time prediction of batch release criteria properties means that in lab measurements and testing are no longer necessary and can be used in conjunction with Fero Labs’s predictions. This will drive productivity as it will enable plants to produce more batches per day as manual and ponderous batch release testing can now be done with Fero Labs during production. This can relieve any laboratory driven process bottlenecks and reduce the total annual lab measurements by as much as 20%, while providing additional visibility into production.
Cost savings
As the need for in lab measurements is reduced, plants save on capital and labor costs. Furthermore, issues with batches detected by Fero can be fixed during production, saving on losses associated with the cost to rework or dispose of out-of-spec batches.
With full adoption of Fero, plant operators can expect up to 10% increase in annual revenue, based on a reduction of costs associated with reworking out-of-spec batches and losses in raw material.
Reduced waste and minimize Scope 1 and 2 footprint
Monitoring plant performance and predicting final product quality enable plant operators to minimize off-specification production, alleviating the operational challenge of managing excess off-spec batches and mitigating issues related to storage, waste, and environmental concerns. Minimizing off-spec batch accumulation through real-time optimization supports more sustainable operations, reducing the plants Scope 1 carbon footprint through waste reduction and lowering its Scope 2 carbon footprint by reducing the processing need to reworking an off-spec batch.
Fero Labs Adoption Timeline
Plant teams can collaborate to set up and deploy Fero Labs. Below is a timeline highlighting typical steps. With Fero’s easy-to-use, no-code interface, this can be achieved in a matter of weeks, not months or years.
Data Requirements
Plant teams can collaborate to set up and deploy Fero. Below is a timeline highlighting typical steps. With Fero’s easy-to-use, no-code interface, this can be achieved in a matter of weeks, not months or years.
Activating This Use Case
Consider our Industrial Use Case Playbooks as inspiration and tactical ideas for your team to align on to maximize the efficiencies of your plant.
Each Playbook has a matching Use Case Blueprint which provides more detailed steps to activate each use case within the Fero Labs platform.
If you’re curious to see these in action please book a free feasibility study with our team!
Together, let us continue to push the boundaries of what's possible, driving towards a future where industrial manufacturing is not just efficient and sustainable but truly transformative in its impact on society and the world at large.
Thank you for joining us on this journey, and we look forward to continuing to partner with you in your pursuit of excellence.
Download the entire Batch Release Testing Playbook to access additional tables and details about this industrial use case.