Use Case Description
Background
Heat exchangers play a crucial role in numerous industrial processes and refineries by enabling efficient heat transfer between fluids. They are typically used in continuous production and are consequently exposed to gradual fouling — the accumulation of unwanted materials on the surface of heat exchangers — which can significantly impair their performance. Since the amount of fouling can be difficult to measure, operators typically monitor it by measuring parameters like pressure drop or (overall) heat transfer coefficient, which serve as indirect measures of the overall fouling behavior in the unit.
Problem
The rate of fouling in heat exchanges vary even under consistent operational conditions. This variability presents a significant challenge for plant operators and managers in scheduling maintenance of heat exchangers and planning operational shutdowns. This lack of understanding of the root causes behind such differences complicates efforts to predict when maintenance is needed.
Prolong heat exchanger lifetime by projecting future values of the heat transfer coefficient and presenting a clear timeline for when heat exchanger maintenance should occur.
If not properly maintained, heat exchangers with high fouling can become a serious operational safety risk, prompting plant operators to default to a cautious maintenance protocol, opting for regular scheduling of maintenance activities. This strategy tends to reduce the operational cycles of the heat exchanger, leading to frequent, often premature, production halts. Such a strategy comes at significant operational costs. Furthermore, the requirement for various cleaning methods ranging from thermal and mechanical to chemical and steam cleaning adds to the complexity and financial burden of upkeep.
Fero Labs Solution
With Fero Labs, plant operators can closely monitor and forecast the heat transfer coefficients of heat exchangers under various operating conditions. More specifically, Fero pinpoints the key operating parameters affecting performance based on root cause analysis and leverages machine learning-based forecasting methods to project future values of the heat transfer coefficient, providing a clear timeline for when maintenance should ideally occur to mitigate significant degradation due to fouling. This proactive approach, can maximize the operational lifespan of the heat exchanger during each operational campaign.
A “Live Fero Asset” for this use case presents the following interactive screen:
- Forecast view: in the top panel, plant managers can monitor past heat transfer coefficients and observe forecasts, with the transition from historical to forecasted data marked by the solid black vertical line. Here, Fero projects how past and current operating conditions and heat transfer coefficients might evolve, highlighting potential increases in fouling that may necessitate maintenance. To aid in decision-making, Fero provides forecasts surrounded by confidence intervals. If operators wish to proactively manage fouling risks, they are guided to schedule maintenance when the forecast’s lower confidence boundary intersects with the lower specification limit, as shown by the dashed orange horizontal line.
- Scenario view: in the bottom panel, plant operators can monitor the corresponding past operational parameters and observe their forecasts. This allows for the adjustment of forecasted values to assess their impact on projected heat transfer coefficients displayed in the top panel. This enables operators to simulate adjustments in operating parameters or set-point values based on anticipated changes. Moreover, this simulation capability supports the exploration of strategic operational adjustments that could extend the heat exchanger’s operational lifespan.
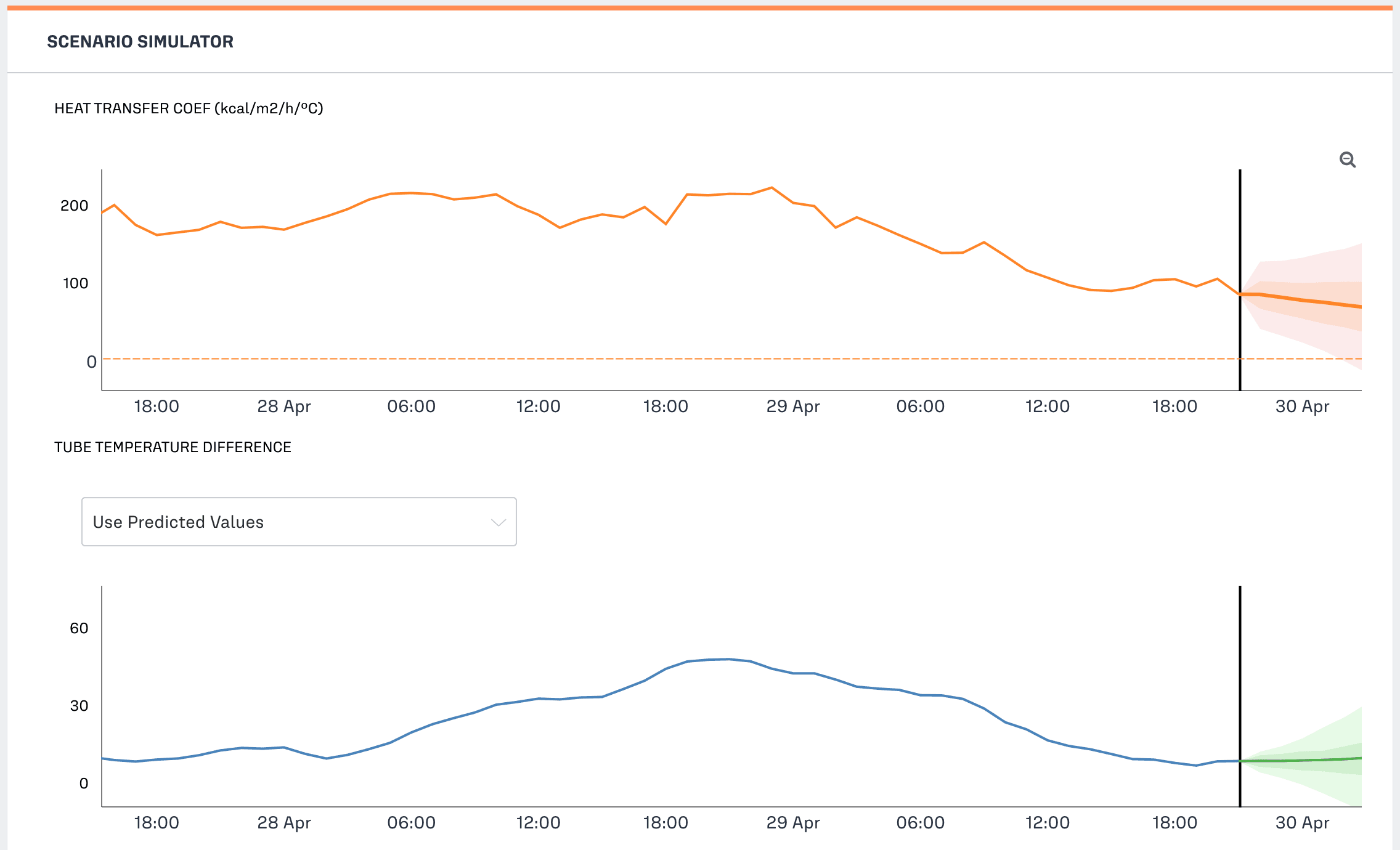
Process & Business Outcomes
Increased profitability by extending heat exchanger lifetime
With Fero providing forecasts for fouling days in advance, process engineers and plant operators can proactively increase profitability by extending heat exchanger campaign durations. Since process engineers and operators gain access to predictions as early as 5 days ahead of time, they can proactively adapt rather than react to fouling caused by dynamic process operating conditions. With full adoption of Fero on the production line, plant operators can achieve up to 20% extension of heat exchanger operational lifetime.
Conduct “what-if” simulations to gauge the effects of process modifications
Fero Assets allow the plant engineers to test hundreds of different “what-if” operating scenarios for future time horizons. This is particularly beneficial when operators possess insight into potential adjustments in operating parameters or setpoint values in the next 5 days and seek to understand their impact on the forecasted heat transfer coefficients. By enabling this level of predictive analysis, operators can identify effective strategies that not only prolong the operational lifetime of the heat exchanger, but significantly enhances overall operational efficiency and minimizes downtime.
Informed decision-making to mitigate unplanned shutdowns
Plant operators can be more confident when deciding to initiate a plant shutdown or make an operational change when heat exchanger fouling rates accelerate. With full adoption of Fero Labs software, plant operators can expect to experience up to 36% decrease in unplanned production shutdowns.
Fero Labs Adoption Timeline
Plant teams can collaborate to set up and deploy Fero Labs. Below is a timeline highlighting typical steps. With Fero’s easy-to-use, no-code interface, this can be achieved in a matter of weeks, not months or years.
Data Requirements
Plant teams can collaborate to set up and deploy Fero. Below is a timeline highlighting typical steps. With Fero’s easy-to-use, no-code interface, this can be achieved in a matter of weeks, not months or years.
Activating This Use Case
Consider our Industrial Use Case Playbooks as inspiration and tactical ideas for your team to align on to maximize the efficiencies of your plant.
Each Playbook has a matching Use Case Blueprint which provides more detailed steps to activate each use case within the Fero Labs platform.
If you’re curious to see these in action please book a free feasibility study with our team!
Together, let us continue to push the boundaries of what's possible, driving towards a future where industrial manufacturing is not just efficient and sustainable but truly transformative in its impact on society and the world at large.
Thank you for joining us on this journey, and we look forward to continuing to partner with you in your pursuit of excellence.
Download the entire Heat Exchanger Maintenance Optimization Playbook to access additional tables and details about this industrial use case.