Use Case Description
Background
Steel wire drawing involves pulling steel wire through progressively smaller dies to reduce its cross-sectional area. Typical steps involve heating, rolling, lubricating, drawing, patenting or annealing, and plating or galvanizing. Steel wires and filaments have myriad uses in the construction, automotive, agriculture, and other industries.
Problem
Minimizing fractures in steel wire drawing is a challenging task. Non-metallic inclusions in steel wire rods can lead to fractures during the drawing process, which cause scrapped production.
Adapting to non-metallic inclusions and other feedstock variability is difficult because hundreds of process parameters affect final wire quality metrics, such as breaking force, tensile strength, and elongation.
Moreover, minimizing the energy and electricity consumption during annealing, patenting, plating, and galvanizing process stages can interfere with quality objectives.
Process and quality engineers operating wire drawing processes must actively trade off scrap rates with production efficiency. Measuring the precise nature of non-metallic inclusions can be impractical, making it unclear how to adapting process parameters during production.
Minimize fractures and energy consumption by adapting to non-metallic inclusions in feedstock and targeting process changes in energy-intensive process stages.
The current solution is to define production set-points based on product grades, ideally with some static adjustment based on feedstock steel cleanliness measurements. These frequently advocate sub-optimal die angle and patenting set points, which results in:
- financial loss due to fractures in final product and unnecessary heat and electricity consumption, and
- environmental cost of incurring Scope 2 and 3 emissions due to wasted energy and scrapped product.
Fero Labs Solution
Wire drawing facilities can use Fero Labs software to minimize the risk of fracture and target low energy consumption while ensuring that breaking force, tensile strength, and elongation KPIs are kept with product specifications.
Worst-case downstream drawing parameters can be used to minimize risk of product re-grades and fracture scrap.
A Live Fero Analysis for this use case presents two screens:
- Detailed View: for production and quality engineers to monitor production and take action at any moment
- Simplified View: for operators on the factory floor, with critical information clearly presented.
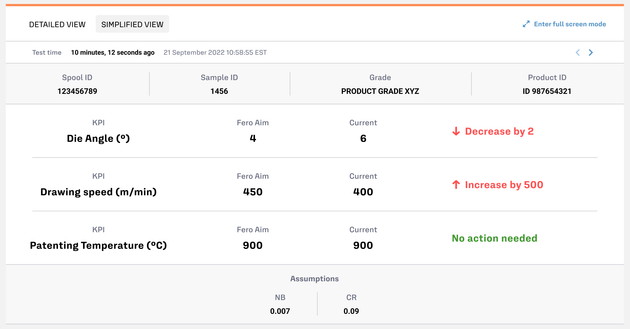
Process & Business Outcomes
Tightened variation of end-of-line mechanical properties
With Fero Labs providing optimal recommendations based on available non-metallic inclusions of feedstock steel rods, steel cleanliness no longer translates to end-of-line mechanical property variation.
Since each spool is optimized to meet its specific quality metrics relative to its specific upstream quality measurements and process set points, breaking force, tensile strength, and elongation measurements become more stable.
With a full adoption of Fero Labs software on the production line, wire drawing facilities can see up to 15% reduction in mechanical property variability, within production grades. Knowing that production will reliably meet its specifications leads to smoother operations.
Reduced risk of production regrades and fracture scrap
With high-grade steelmaking, fractures can be challenging to minimize. Even though non-metallic inclusion measurements may not be fully comprehensive, Fero can optimize production parameters, such as drawing die angles and patenting temperatures, to minimize risk of fractures.
With Fero optimizing each spool based on its cleanliness properties, wire drawing facilities can expect up to a 25% decrease in scrap and regrade rates.
Measurable cost savings from minimizing energy and electricity
Static recipes for product grades lead operators to patenting, plating, and galvanizing set-points that consume unnecessary amounts of energy.
With Fero optimizing for production cost, while maintaining stability of end-of-line mechanical properties, operators can minimize temperatures and currents at key stages during production.
With a full adoption of Fero on the production line, wire drawing facilities can expect up to 3% cost savings in electricity consumption.
Commensurate Scope 2 and 3 carbon footprint minimization
The minimization of fracture tackles the tricky problem of reducing Scope 3 emissions. Additionally, any reduction of energy and electricity consumption carries a commensurate reduction in Scope 2 emissions.
Directly addressing the objectives above can reduce the carbon footprint of production by up to 15%. Fero Labs can provide reporting capabilities that directly track and account for this reduction.
Fero Labs Adoption Timeline
Wire drawing facilities with specialized teams can collaborate to set up and deploy Fero. Below is a timeline highlighting typical steps. With Fero’s easy-to-use, no-code interface, this can be achieved in a matter of weeks, not months or years.
Data Requirements
Learn what data is required for this use case, and in which format it can be provided. From your feedstock chemistry data to your fracture measurement data, download the Playbook to access information on ideal data sources, formats, and time periods.
Activating This Use Case
Consider our Industrial Use Case Playbooks as inspiration and tactical ideas for your team to align on to maximize the efficiencies of your plant.
Each Playbook has a matching Use Case Blueprint which provides more detailed steps to activate each use case within the Fero Labs platform.
If you’re curious to see these in action please book a free feasibility study with our team!
Together, let us continue to push the boundaries of what's possible, driving towards a future where industrial manufacturing is not just efficient and sustainable but truly transformative in its impact on society and the world at large.
Thank you for joining us on this journey, and we look forward to continuing to partner with you in your pursuit of excellence.
Download the entire Fracture and Energy Minimization for Wire Drawing Use Case Playbook to access additional tables and details about this industrial use case.