Use Case Description
Background
In petroleum refineries, residual fuel oils from crude distillation units, also referred to as heavy fuel oils (HFOs), are blended with various light oils to improve quality. These additives, known as cutter stock, encompass low viscosity oil and oil-derived products such as kerosene, olefins, diolefins, light cycle oils (LCOs), and diesel.
The main objective of integrating these components into HFOs is to reduce its viscosity to target specifications, allowing the resulting fuel blend to be categorized, marketed, and sold as value-add fuel products.
Problem
The value of cutter stock is high and often more valuable than the resulting fuel oil, motivating plant operators to minimize its use in the blending process while still meeting desired viscosity specifications.
This requires a delicate balance: insufficient addition of cutter stock can leave the HFOs overly viscous and unsuitable for sale, whereas adding an excessive amount of cutter stock can lead to major monetary losses.
Predict final fuel oil viscosity and minimize the quantity of cutter stock required to save costs.
To ensure the viscosity of the final blend meets required specifications, plant operators periodically sample the fuel oil blend during production and measure its viscosity. In general, the lack of access to KPI data for prolonged periods forces operators to rely heavily on their expertise and judgement during the blending process.
This approach, although beneficial for repurposing and enhancing HFOs, can lead to overuse of cutter stock by up to 15% if the process operator believes that fuel oil specifications are not being met.
Fero Labs Solution
A well configured Fero Labs analysis can be used accurately predict final fuel oil blend viscosity and learn the important factors that impact it. Based on the predictions of final viscosity and the properties of the cutter stock (kerosene and LCO), Fero can then optimize to achieve viscosity within spec while minimizing the amount of total cutter stock needed. The result of Fero’s optimization is clear recommendations to make process changes in order to achieve viscosity goals.
A Live Fero Analysis for this use case presents two screens:
- Detailed View: for production and quality engineers to monitor production and take action at any moment. In this example we see that Fero predicts final fuel oil viscosity based on current conditions and amount of kerosene and LCOs. If the viscosity is predicted to be well within spec (as seen below), Fero will recommend reducing the amount of each cutter stock in the process while constraining the total wt% of cutter stock. These changes will minimize total cost of cutter stock while keeping viscosity in specifications.

- Simplified View: for plant operators with critical information clearly presented to prompt them to make changes to the process to achieve the desired viscosity while minimizing the cost of cutter stock usage.
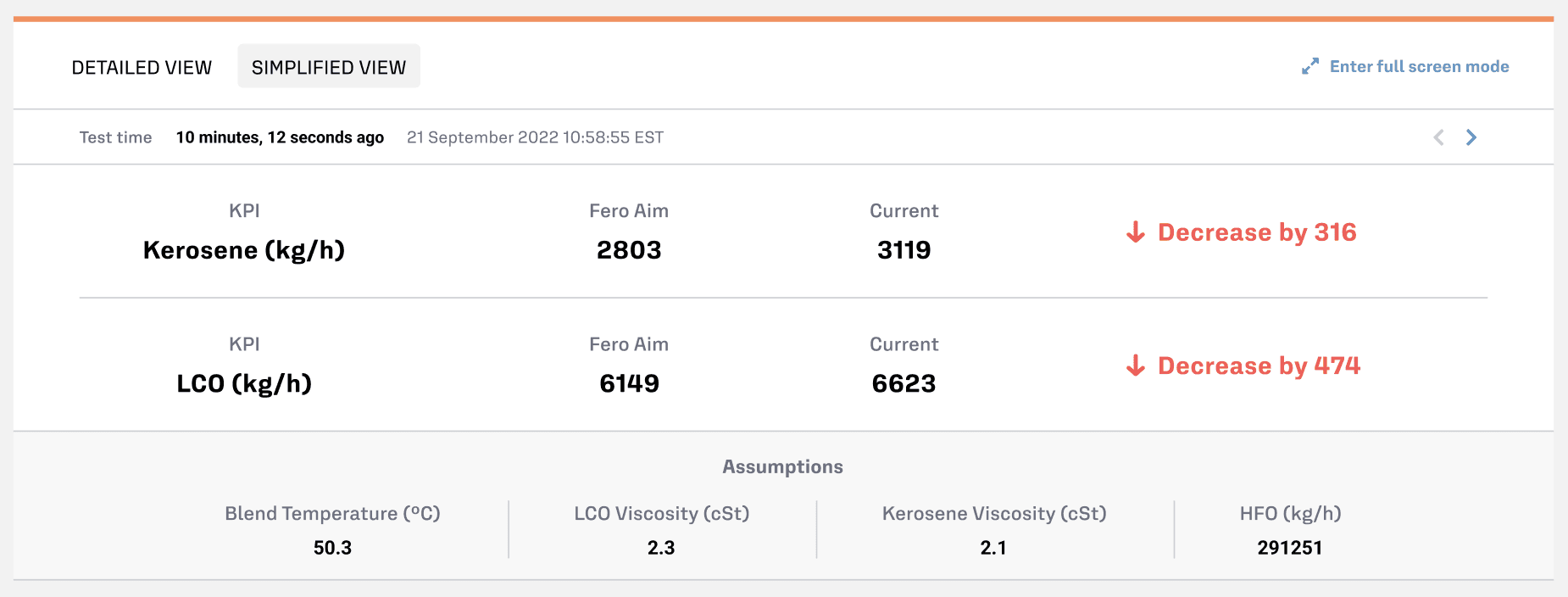
Process & Business Outcomes
In-process optimization and commensurate cost minimization
When deployed, Fero considers the varying feed stock characterizations and process conditions throughout the crude distillation process to make predictions for blend viscosity. Operators receive real-time, cost-efficient recommendations for adjusting the process parameters to minimize the cost of cutter stock while maintaining the fuel oil blend viscosity within specification. These recommendations also take into account time lags in measurements made at different stages of production. Optimizing viscosity by just 1 centistoke is projected to reduce cutter stock usage by up to 15%, resulting in significant cost savings.
Reduced lab measurement frequency
By adopting Fero as a virtual soft sensor, refineries gain access to estimates for fuel blend viscosities at regular intervals, reducing dependence on laboratory measurements. This approach can alleviate bottlenecks caused by laboratory-dependent measurements and decrease the total annual lab measurements by as much as 20%, enhancing visibility into production.
Reduced HFO accumulation and minimize environmental footprint
Adjusting the amount of cutter stock added enables operators to reduce the volume of HFOs requiring further processing or rework, alleviating the operational challenge of managing excess HFOs and mitigating issues related to storage, waste, and environmental concerns. Minimizing HFOs accumulation through real-time optimization supports more sustainable operations, reducing the refinery’s environmental footprint.
Fero Labs Adoption Timeline
Plant teams can collaborate to set up and deploy Fero Labs. Below is a timeline highlighting typical steps. With Fero’s easy-to-use, no-code interface, this can be achieved in a matter of weeks, not months or years.
Data Requirements
Plant teams can collaborate to set up and deploy Fero. Below is a timeline highlighting typical steps. With Fero’s easy-to-use, no-code interface, this can be achieved in a matter of weeks, not months or years.
Activating This Use Case
Consider our Industrial Use Case Playbooks as inspiration and tactical ideas for your team to align on to maximize the efficiencies of your plant.
Each Playbook has a matching Use Case Blueprint which provides more detailed steps to activate each use case within the Fero Labs platform.
If you’re curious to see these in action please book a free feasibility study with our team!
Together, let us continue to push the boundaries of what's possible, driving towards a future where industrial manufacturing is not just efficient and sustainable but truly transformative in its impact on society and the world at large.
Thank you for joining us on this journey, and we look forward to continuing to partner with you in your pursuit of excellence.
Download the entire Cutter Stock Additive Minimization Playbook to access additional tables and details about this industrial use case.