Use Case Description
Background
Several steel surface defects, such as longitudinal and off-corner cracks, originate from the continuous casting process. Casting speeds and temperatures, cooling rates, and the chemical composition of different steel grades can contribute to the problem, leading to reworked or even scrapped production.
Problem
Controlling continuous casting to maintain stable production conditions while minimizing surface defects is challenging. The variability in the chemical composition of different grades of steel and equipment age, along with desired casting temperature and speed set points can lead to increased surface defect rates.
Process engineers and operators in charge of continuous casting processes define set points such as casting temperatures, speeds, mould water flows and pressures to maintain high quality and stable casting of steel into semi-finished products (blooms, ingots, billets, slabs, etc.). These are set based on solidification profiles, tundish temperatures and other process parameters, and rarely reflect variations in chemistry.
Minimize surface defects during continuous casting by adaptively controlling casting parameters on a batch-by-batch basis in real time.
The current solution involves physics-based models and following historical best practices. These do not capture the full properties of each batch being cast. This approach leads to:
- financial loss due to rework and scrap of products with too many surface defects,
- environmental cost of incurring Scope 1 and 2 emissions due to the unnecessary rework or scrapping of produced steel.
Fero Labs Solution
Continuous casting process operators can use Fero Labs software to minimize surface defects by adapting to each batch and learning over time. Operating limits for caster set points can be configured within the software to enable safe recommendations that operators can follow with confidence.
A Live Fero Analysis for this use case presents two screens:
- Detailed View: for production engineers to monitor production and direct action plans at any moment.

- Simplified View: for continuous casting process operators, with critical information clearly presented.
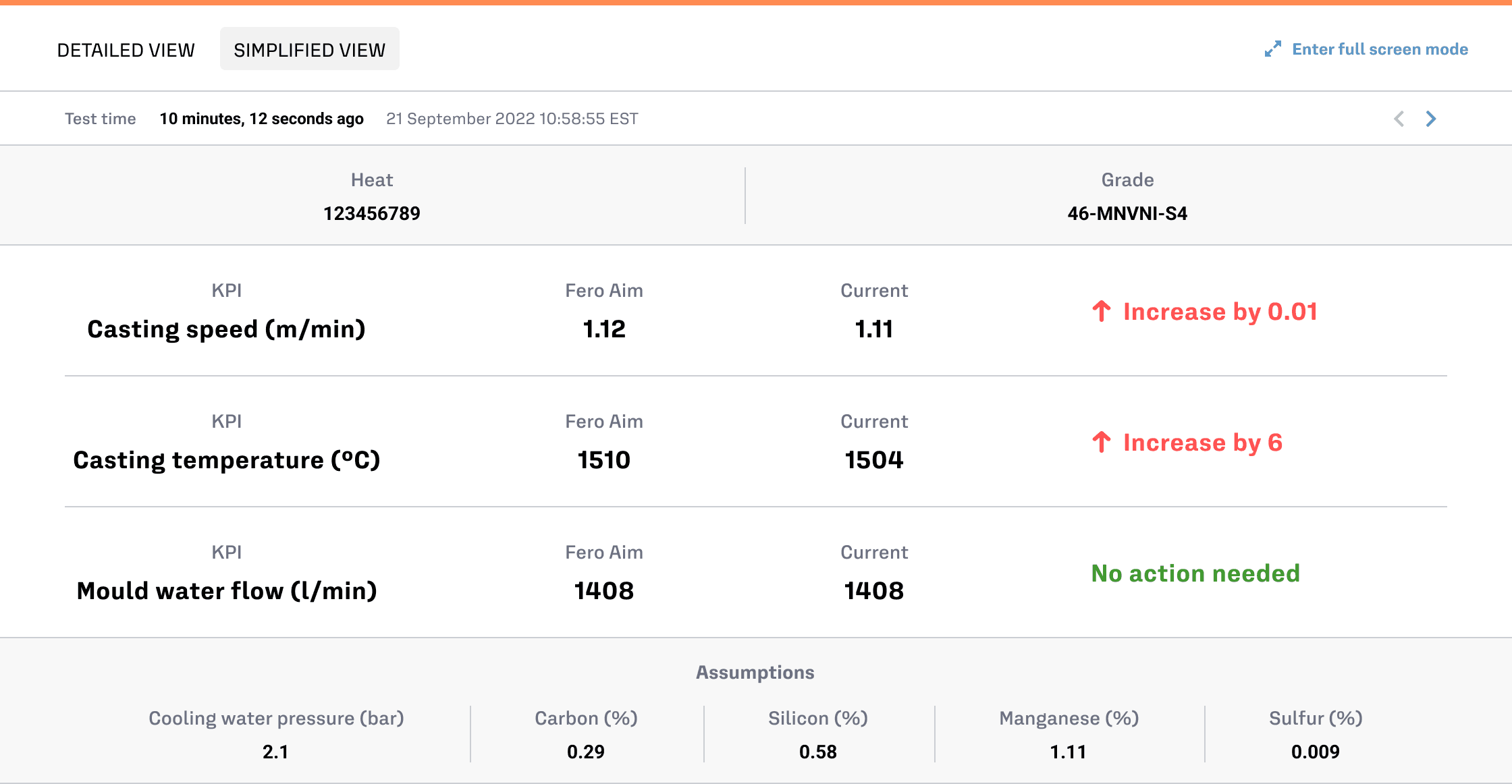
Process & Business Outcomes
Significant reduction of scrap rates
With Fero Labs providing optimal recommendations for continuous caster parameters, chemistry and caster temperature variability no longer translate to increased surface defects. Since each batch is optimized to safely minimize surface defect rates relative to its specific chemical composition and casting temperature, continuous casters can expect a 18% decrease in scrap rates.
Decreased severity of surface defects
Fero Labs software not only minimizes the probability of surface defects, but also recommends operational changes that reduce the length of surface defects. With a full adoption of Fero Labs software on the production line, continuous casters can see up to 40% reduction in average surface crack lengths. Knowing that production will reliably meet its specifications leads to smoother operations.
Measurable cost savings minimizing rework
Static casting operating procedures for product grades lead to unnecessarily high surface defect rates. Some of these products can be reworked, which incurs additional rework costs, both in personnel and in energy. With a full adoption of Fero on the production line, continuous casters can expect up to 15% reduction in rework of semi-finished products with mild surface defects.
Commensurate Scope 1 and 2 carbon footprint minimization
The minimization of scrapped and reworked product directly translates to a commensurate reduction of Scope 1 and 2 emissions. Since more than half of EAF steelmaking’s carbon footprint falls into Scope 1 and 2, a reduction here can reduce the carbon footprint of production by up to 10%. Fero can provide reporting capabilities that directly track and account for this reduction.
Fero Labs Adoption Timeline
Plant teams can collaborate to set up and deploy Fero Labs. Below is a timeline highlighting typical steps. With Fero’s easy-to-use, no-code interface, this can be achieved in a matter of weeks, not months or years.
Data Requirements
Plant teams can collaborate to set up and deploy Fero. Below is a timeline highlighting typical steps. With Fero’s easy-to-use, no-code interface, this can be achieved in a matter of weeks, not months or years.
Activating This Use Case
Consider our Industrial Use Case Playbooks as inspiration and tactical ideas for your team to align on to maximize the efficiencies of your plant.
Each Playbook has a matching Use Case Blueprint which provides more detailed steps to activate each use case within the Fero Labs platform.
If you’re curious to see these in action please book a free feasibility study with our team!
Together, let us continue to push the boundaries of what's possible, driving towards a future where industrial manufacturing is not just efficient and sustainable but truly transformative in its impact on society and the world at large.
Thank you for joining us on this journey, and we look forward to continuing to partner with you in your pursuit of excellence.
Download the entire Caster Optimization for Surface Defect Reduction Playbook to access additional tables and details about this industrial use case.