Fero founder Berk Birand discusses what manufacturers learned in 2021, and the future of global manufacturing in 2022, with Industry Today:
What did manufacturers learn in 2021, coming out of the pandemic?
For the first time, manufacturers are recognizing the urgent need to be adaptive and agile with their production.
When the pandemic began, most manufacturers had to aggressively cut production because demand disappeared and they wanted to keep their workforce safe. But this year, many manufacturers saw demand skyrocket, fueled by suppressed demand and government spending (like the infrastructure bill in the US).
Scaling production quickly based on demand is not something manufacturers usually think about. They tend to rely on Six Sigma and similar management approaches, which emphasize reducing variability in production. Thus, the past year’s incredible variability in demand caught manufacturers off-guard. Now, we’re seeing many turn to technologies like digitization and ML in order to increase their agility.
Did anything happen in 2021 that surprised you?
The sudden increase in demand for sectors like steel and truck OEMs were very surprising. Many factories went from being shut down, to running around the clock to satisfy demand.
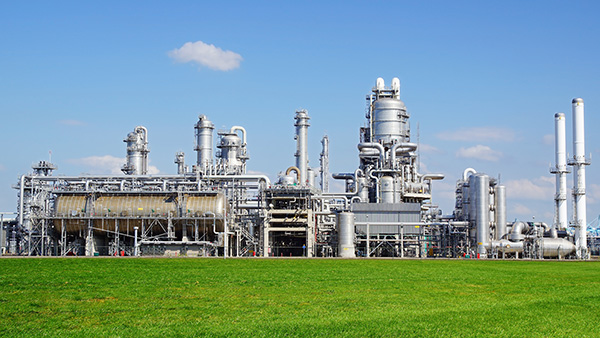
What do you expect for manufacturing and technology in 2022?
This year, climate change will get an even bigger spotlight. Many boards are pushing for aggressive sustainability goals (e.g, become carbon-neutral by 2050). So you can expect to see a shift in tech adoption as managers scramble to comply with these top-line priorities.
At Fero, we’re also seeing more and more interest in the explainable aspect of machine learning. Manufacturers now largely acknowledge that they need to invest in digital solutions like ML to turn their data into a competitive advantage–particularly with the pandemic, which really hit home the need for agile production. However, many have been burned by “black-box” ML solutions, which don’t explain the root cause of production issues, don’t scale well to industrial settings, and ultimately fail to drive value. So we’re seeing increased interest in transparent solutions like Fero Labs, which are easy for engineers to use and trust.
What do you see for the future of manufacturing regarding climate change?
Climate change continues to be a major focus for global industrial companies. As mentioned before, many boards are pushing for aggressive sustainability goals. ML will continue to play a key role in allowing companies to make the most of their capital assets. For example, cement companies are using ML to start using alternative fuels without hurting production. Steel companies are using ML to reduce raw material consumption. CPG companies are using it to increase throughput while keeping energy consumption constant.
What areas or strategies will cool down in 2022?
In recent months, there have been several articles that started bursting the hype cycle of “AI” (e.g., the IEEE articles). Those much-hyped approaches typically involved pushing deep learning into the industrial sector. But now, many are realizing that these black-box methods are rarely the correct solution to problems.
Instead, one of the major requirements that is coming up is trust. No technology can be adopted by factories worldwide without engineers trusting it–no matter how “intelligent” it sounds.
Do you anticipate labor shortages to continue in 2022?
Yes, definitely. This is one huge area where machine learning can be transformative. By integrating explainable machine learning software into the production process, manufacturers can reduce their dependence on operators with specific qualifications and experience.
At the same time, they can use machine learning to teach employees new skills faster.
With a “digital twin” (i.e. a virtual model of the factory floor), both entry-level and experienced engineers can build experience and test their decision-making skills in various hypothetical scenarios, without sacrificing either working time or quality of physical products. This allows factories to hire workers without the necessary level of experience for a particular role and efficiently bring them up to speed, even before starting their roles.
Originally published in Industry Today.